We’ve seen a number of economic factors collide recently: steep drops in demand and prices across basic commodities including oil and petrochemical products, uncertainty across global economies, and mixed actions from economic and political leaders of many countries. This can be attributed to the varying degree of spread of COVID-19 across the globe. All these conditions have placed companies under economic stress, especially those in the process industry struggling to maintain sales and output levels. Companies are taking radical actions to reduce capital and operational expenditure. These economic pressures can be taxing on all areas of a business, but especially on the production floor‐level operations.
Cost‐cutting directives are coming from the executive levels, demanding a significant reduction in expenditures while maintaining ongoing production. While all areas of a company feel the impacts, key process safety impacts are experienced on facility floors. A slight slip in the level of process safety endangers operators, maintenance personnel, and their supervisors. During these times of extreme economic pressure, it is imperative that process safety management remains in full-fledged effect. ‘Safety first’ must be an overriding motto and an unflinching standard for process manufacturing industries.
Numerous operating companies globally are faced with major unparalleled challenges. Some of the steps taken to address these challenges can compromise process safety leading to hazardous conditions. This article is intended to serve as a reminder of the impacts of cost cutting decisions taken amidst the pandemic and to present solutions to combat the loss of process safety effectiveness.
Challenges
1) The pandemic has reduced operational staffing and in certain cases, led to shutdown of facilities or suspension of operations for a period of time. Restarting operations is a non-standard activity and requires more vigilance than normal operations. Limited availability of resources and staff on site can put strict adherence to standard operating procedures at risk.
Solution: A review of start-up SOPs and their associated comprehensive checklists should be done with reduced staffing impacts considered. This can help ensure safety even with workforce turnover. If a reduction in workforce is inevitable, updated documentation will assist operations, maintenance and inspection, with incident prevention. OSHA PSM provides guidance on these requirements/procedures. One criterion is the presence of alarms independent of an initiating event, which alert operators of abnormal events. Both not having the appropriate alarms and having so many that there is “alarm overload” can create safety issues.
2) After being shut down, most companies try returning to full capacity to maximize operational cost effectiveness. This process of reaching maximum production can lead to safety data point incursion or deviation of parameters at higher limits. Over pressure scenarios need to be considered to a much higher level for start-ups and when pushing plant limits, particularly if debottlenecks or equipment enhancements were done during shut down. API standard 521 allows credit for operator intervention to prevent overpressure scenarios from happening. If such credit has not been accounted for in the original design, limited availability of resources can create a new “alarm overload” situation for remaining personnel. This would exacerbate the existing situation significantly, leading to more overpressure scenarios where pressure within equipment exceeds design values.
Solution: Dedicated Process Safety Management and Risk Management personnel should consider implementing automated monitoring systems to capture abnormal deviations in key operating parameters like pressure, temperature (min./max.), ∆P’s, levels, control valve limits etc. While limits and alarms are set in the DCS system, machine learning and multivariate analysis can provide insights about process stability and abnormal process behavior much sooner than a specific alarm on excessive pressure or temperature. Integrated data flow and analysis provides visibility on the end-to-end cash conversion cycle, helping companies remain cost-effective and astute on the day-to-day, while still ensuring worker and plant safety.
3) Cash flow reduction from lower product consumption/sales has resulted in budget cuts including process safety initiatives. Ongoing evaluation of relief system design per OSHA guidelines is being put on hold, slowed down, or deferred to next cycle in many companies.
Solution: In these trying times, utilizing labor rate disparities based on geographical location can be a key parameter to address these issues. Outsourcing to companies that provide high value services while upholding quality is a cost-effective solution. This would fall in line with intended budget cuts and bridge the gap further to continue with the evaluation of relief system designs rather than slowing it down or deferring to a later date.
4) Equipment Health/Reliability — The upkeep of plant MOCs (Management of Change) and PSSRs (Pre-start up safety review) per OSHA guidelines is likely to decrease due to limited availability of on-site resources and staff. Assumptions that corrosion did not take place during a 30–60 day operational suspension, and that a PSSR is not needed is ill advised.
Solution: Before starting up again, companies should follow metallurgical inspection guidelines. Additionally, utilizing fault diagnostic applications within processes are beneficial. Early fault detection and failure prevention software solutions with live analytics and dashboards provide enhanced failure predictions and help identify anomalies in real-time. Having access to a multidisciplinary team of engineers (either in-house or outsourced) to evaluate the impact of change is also helpful. This team can go through the detailed description of the MOC and perform a thorough overpressure scenario analysis to check the adequacy of the existing overpressure protection system. This process will require integration with MOC systems.
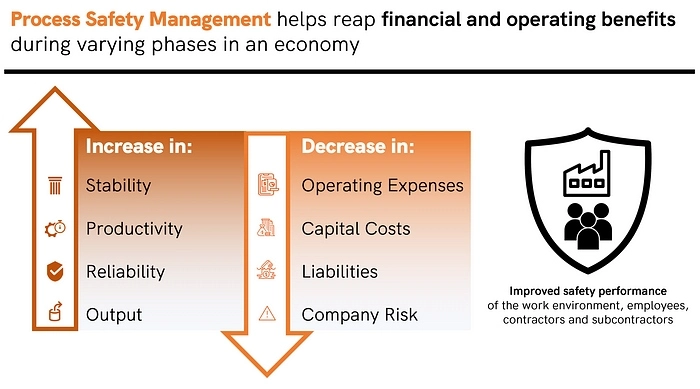
Here’s how Ingenero can add value!
Ingenero is one of the foremost multinational companies that provide process safety management services globally across various sectors. Our process safety experts, process risk professionals, engineers, and auditors are among the top industry specialists, and possess vast experience in the field of process management and safety. This is evident from the trust and confidence of other industry organizations, public works, government agencies, and various private companies handling extremely hazardous chemicals. With over 1.1 million man-hours of experience in analyzing relief system design for the past 16+ years, Ingenero engineers have uncovered numerous design deficiencies (about 25–40% design deficiencies or flaws in original design). Some of these deficiencies, if left unattended, can significantly compromise overpressure protection, leading to loss of containment or even vessel rupture. Ingenero’s multidisciplinary team can help prevent / mitigate many such scenarios during these testing times.
Here are some of the services we provide:
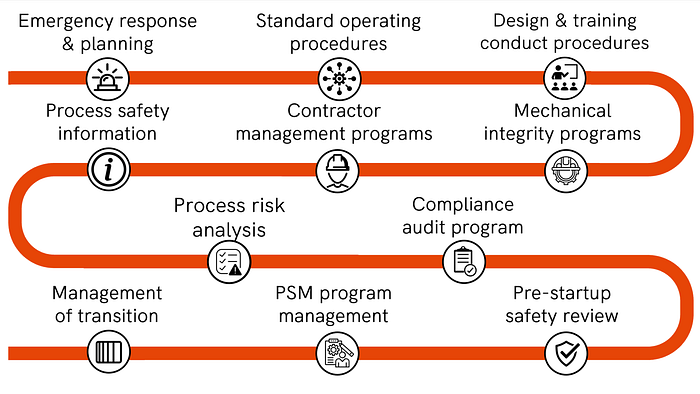
Ingenero serves as a process safety consultant using comprehensive solutions that streamline processes. We assist in encapsulating chemicals and other hazardous materials to reduce emissions and risks and thereby improve the security and safety of your workers and assets. Ingenero with its experience and engineering excellence can be a key option to implement robust Process Safety Management and ensure full compliance with guidelines such as OSHA PSM.
For more information around how we can help your process safety management, reach out to us at usa@ingenero.com or visit our website www.Ingenero.com.